Understanding Seawall Costs: A Practical Guide for Budgeting
Seawall construction costs vary based on location, materials, size, and permits. Factors like labor, equipment, and design influence total expenses.
Discover the expenses of building seawalls in this detailed guide. Seawalls are essential for safeguarding coastal areas, and their costs depend on factors like materials, labor, equipment, permits, etc. Knowing these components is vital for effectively budgeting your seawall project.
Disclosure: This site earns commissions from listed merchants at no cost to you. Thank you!
The Basics of Seawall Construction
Bulkheads and seawalls, although similar, serve different purposes.
While both are constructed to protect shorelines, bulkheads are primarily designed to hold back soil on a bank or cliff, whereas seawalls are built to mitigate the impact of waves.
Materials Used in Seawall Construction
Seawalls can be made from a wide range of materials, each with its own strengths and weaknesses.
Sign up for email updates & get our list of 5 underrated emergency tools under $50
Vinyl
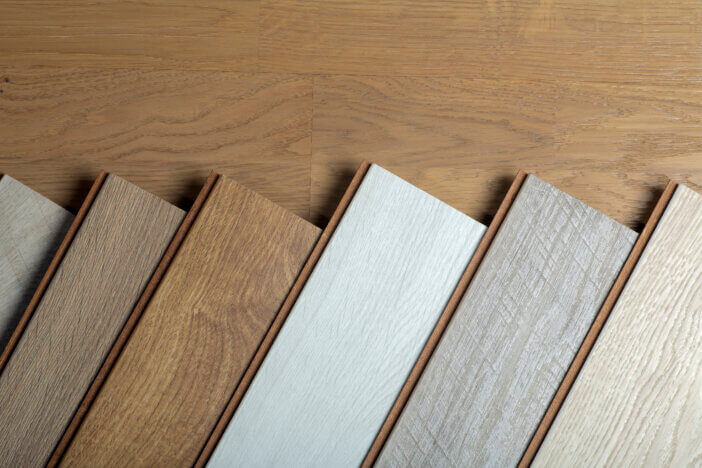
Vinyl is a popular choice due to its durability and resistance to rot and corrosion. It is also lighter and easier to install than other materials.
Wood
Wood is a traditional material for seawalls, but it has lost favor in recent years due to its vulnerability to rot and insect damage.
Metal
Metal, particularly steel, is commonly used because of its strength and ease of installation. Steel can last more than 25 years with proper care and maintenance to avoid corrosion.
Concrete
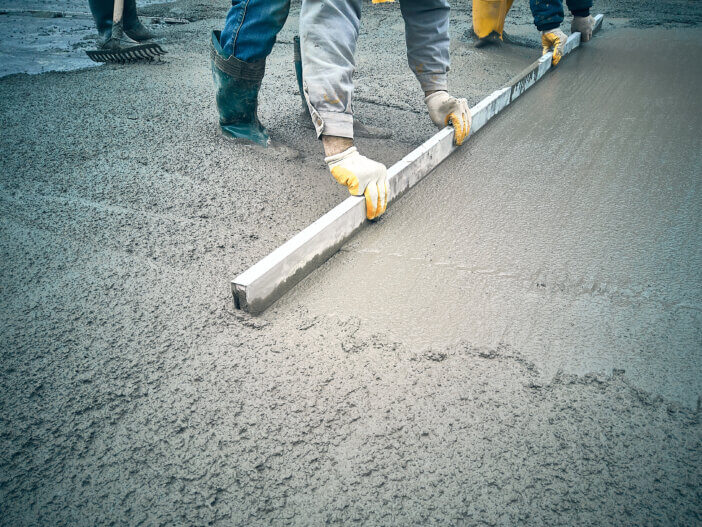
Reinforced concrete is another common material for seawalls because of its strength and durability.
Concrete seawalls can last up to 100 years or more, making them a long-term solution for coastal protection.
Design and Engineering Considerations
The design and engineering of a seawall depend on its purpose, the local environmental conditions, and the resources available.
Factors such as wave height, wind velocity, and the distance from the shoreline to the water’s edge can influence the length and height of the seawall.
The Role of Permits in Construction
Constructing a seawall often requires obtaining permits from local authorities.
These regulations ensure that the construction process adheres to environmental laws and safety standards.
Cost of Seawall Construction
Factors Influencing the Cost
The cost of building a seawall can vary widely depending on several factors.
These include the location of the seawall, the materials chosen, the complexity of the project, and the local regulations and permit requirements.
Location
The site of the proposed seawall can greatly influence the overall cost.
For instance, waterfront properties in urban areas might have higher costs due to increased labor and material prices.
Size, Height, and Length of the Seawall
The dimensions of the seawall are directly proportional to the cost.
A larger, taller, and longer seawall will inevitably require more materials and labor, thereby increasing the total cost.
Foundation Requirements
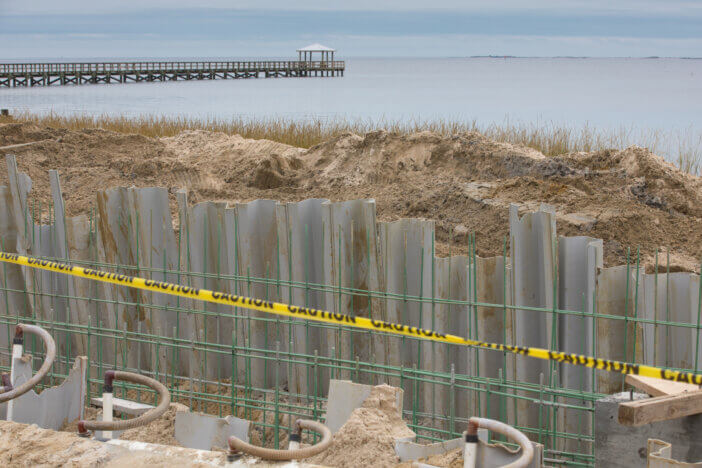
The type of foundation required for the seawall can also affect the cost. More complex foundations may require additional excavation, specialized materials, and more labor.
Erosion Levels
The extent of coastal erosion at the site could also impact the cost.
If the erosion levels are high, additional measures might be needed to stabilize the area before constructing the seawall, adding to the overall expense.
Coastal Protection Needs
The level of coastal protection required can influence the design and construction methods of the seawall, which could add to the cost.
This includes considerations like projected sea-level rise and the potential impact of severe weather events.
Breakdown of Costs
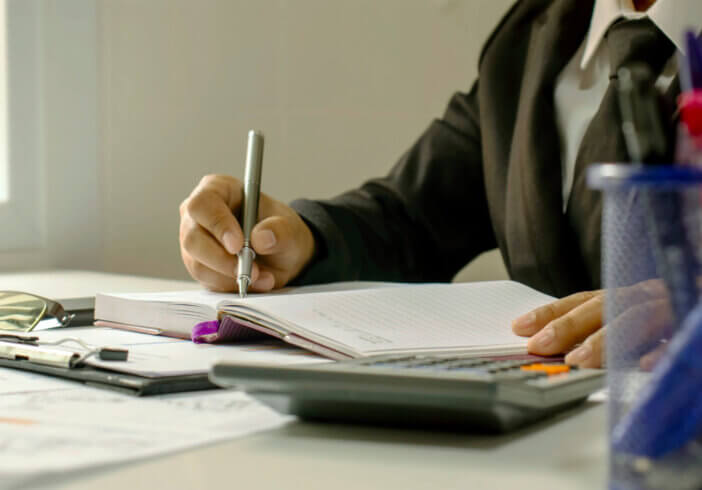
Understanding the breakdown of costs associated with seawall construction can help in better budgeting for the project. Here are some of the primary cost components:
Materials
The choice of materials significantly influences the overall cost. For example, steel is more costly than wood, but it offers greater durability and longevity.
Labor
The cost of labor can vary depending on the complexity of the project and local labor rates. Skilled labor is essential for the successful completion of a seawall project, and their costs should be factored into the budget.
Equipment
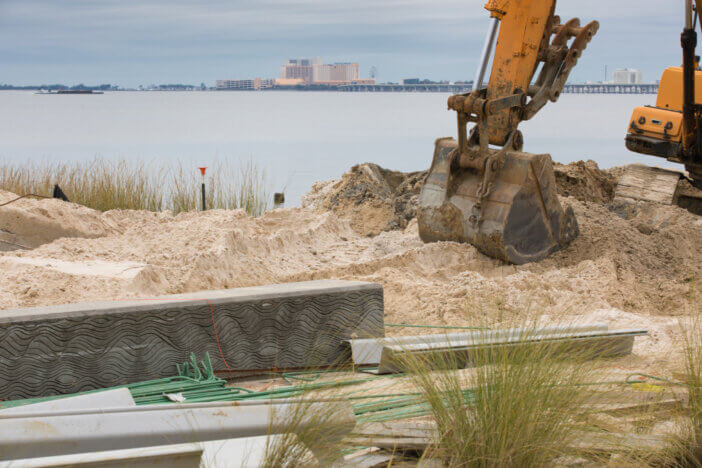
Specialized equipment may be needed to excavate the site, transport materials, and construct the seawall. The cost of equipment rental can range from $100 to $600 per day.
Permits
Permit fees can add to the cost of the project. It’s important to check with local authorities to understand the permit requirements and associated fees.
Budgeting for Your Seawall Project
Budgeting for a seawall project involves considering all the costs mentioned above. A small seawall project may cost as little as $5,000, while a large one may run into millions of dollars.
Therefore, it’s crucial to conduct a thorough analysis to ensure the project stays within budget.
Choosing the Right Contractors
What to Look for in a Contractor
When choosing a contractor for your seawall project, consider their experience in similar projects, their reputation, and their understanding of local regulations and environmental conditions.
Always ask for references and verify their credentials before hiring.
Bidding Process and Project Management
The bidding process helps in selecting the best contractor for the job. After receiving bids from multiple contractors, review their proposals carefully to determine which one offers the best value.
Once the project begins, effective project management is key to ensuring the work is completed on time and within budget.
Durability and Maintenance of Seawalls
Lifespan of Different Materials
The lifespan of a seawall depends largely on the materials used and the maintenance performed.
Concrete seawalls can last up to 100 years, while steel seawalls have a shorter lifespan, typically around 20 to 25 years.
Vinyl seawalls, with proper installation and maintenance, can last for several decades.
Routine Maintenance Tasks
Regular maintenance is crucial to prolonging the lifespan of a seawall.
This includes routine inspections for any signs of damage or deterioration, prompt repairs, cleaning to prevent the accumulation of debris, and maintaining the drainage system.
Environmental Impact of Seawalls
Sustainable Choices for Seawall Construction
While seawalls are necessary for coastal protection, their construction can have environmental impacts.
However, there are sustainable choices available such as using recycled or locally sourced materials.
Another sustainable approach is the creation of living shorelines, which integrate natural elements like marsh grasses or oyster shells, offering both coastal protection and habitat restoration benefits.
Using Crushed Concrete Aggregate or Stone as Backfill
Backfilling with crushed concrete aggregate or stone can also be a more sustainable choice.
These materials are often reclaimed from other construction projects, making them a more environmentally friendly option.
Mitigating Negative Environmental Impact
Efforts should be made to mitigate the negative environmental impact of seawall construction.
This could include measures like controlling sediment runoff during construction, restoring disturbed habitats after construction, and regular monitoring of the site for any adverse environmental effects.
FAQs about Seawall Construction
What is the cheapest way to build a seawall?
The cheapest way to build a seawall largely depends on the site’s specific conditions.
However, generally speaking, using locally available materials and minimizing the size and complexity of the wall can help reduce costs.
How much does a sea wall cost?
The cost of a seawall can vary widely depending on factors like location, materials used, and project complexity.
On average, seawall costs range from $150 to $600 per linear foot, with total costs ranging from $15,000 to $60,000 for a typical residential project.
Can you build a seawall yourself?
While it’s technically possible to build a seawall yourself, it’s generally not recommended unless you have significant experience in construction and engineering.
Improperly built seawalls can fail, causing even more damage to the shoreline and potentially leading to costly repairs.
What are the disadvantages of a sea wall?
While seawalls provide crucial defense against coastal erosion and flooding, they can also have some downsides.
For instance, they can disrupt natural coastal processes, alter habitats, and create downstream erosion problems.
They also require ongoing maintenance and eventual replacement.